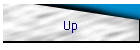
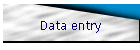
| |
The simplicity of the input
table approach has two major benefits:
- Setting up operations and linking them in this manner means that any changes to
upstream data are automatically incorporated in the calculation process.
- The system is extremely flexible and can very easily handle complicated procedures such
as networks and recycling loops (both closed and open-loop), which cannot readily be
handled by spreadsheet-based calculation tools.
Preparing data for entry
A significant amount of work is often needed before data
obtained from plant operators can be entered into any computer model. The tasks that must
be undertaken in order to enter data in the Boustead Model can be broken down into a
series of three separate stages:.
- conversion of reported quantities to a common base;
- normalisation of data to some suitable parameter;
- identification of code numbers for the inputs and outputs
The Boustead Model predominantly uses the SI system of units
although there is no reason why other units cannot be used. The first thing that any user
must do is to convert data received from plant operators into acceptable units: a program
in the Boustead Model is available to assist this process. Once the units are corrected,
it is necessary to choose some unit for the output of the unit operation. Most commonly
the best units are kg for materials processing operations which yield a flow of materials
and 1, 100 or 1000 units when the operation yields artifacts.The final stage of the data
preparation process is to identify the code numbers corresponding to the various inputs
and outputs for this unit operation and again a program is included in the software to
assist in this task. Table 2 below shows the sequence of events needed to process plant
data relating to the manufacture of a hypothetical product X.
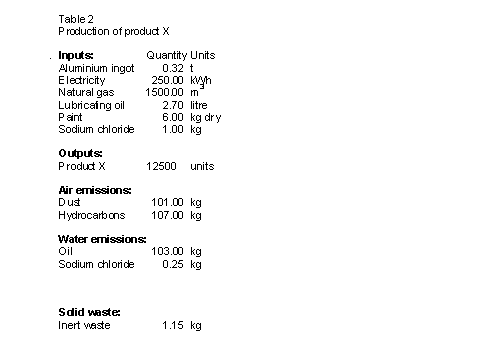
Top of page Data entry
|